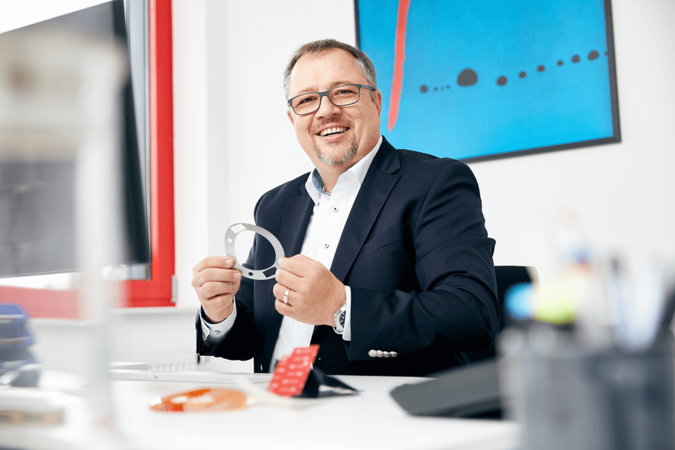
On our rotary die-cutters we can process films, nonwovens, foams, fabrics and laminates in dimensions up to 350 x 500 mm and a maximum roll diameter of 350 mm. Material thicknesses from 0.050 to 2 mm are possible.
What does this manufacturing process actually stand for? Instead of punching mainly against a plate, as was previously the case, we can now offer you the advantages of an interlocking die. Depending on the design the male-female tool actively removes the waste pieces from the punching zone, thus reliably preventing contamination of the product.
With part sizes up to 140 x 140 mm in male-female punching operation and up to 200 x 300 mm for mere punching operations, we cover almost all market requirements with this next stage in manufacturing processes.
Challenge us with even more complex components!
On our stroke die cutters we can process films, nonwovens, foams, fabrics and laminates in dimensions up to 500 x 500 mm and a maximum roll diameter of 350 mm. Thicknesses from 0.050 to 2 mm can be processed - depending on the material properties.
Our all-in-one system is specifically designed for processing roll materials. The production center has a technically sophisticated and complex laser with cutting, marking and micro-perforating functions as well as a separate laminating and grid-off station. Paper, PET film, polypropylene film and Teonex®, to mention only few materials that can be processed on the machine.
Starting from the log roll, we cut adhesive tapes on our computer-controlled cutting machines to the width you specify - regardless of whether you want to realize finest spacings with narrow rolls or to protect the insulation with a wide strip.
Thanks to its independent edge controls, the high-speed lamination winder has the ability to join two materials with a perfect fit; even liner primary materials can be processed without any problems. Depending on the material thickness, lengths of several hundred meters can be produced. In this way, we can enable material combinations according to customer requirements that are otherwise not available on the market.
More and more of our customers want parts that can be used directly in production without further handling. We meet these requirements with our advanced bending technology that ensures only minimal intervention in the material structure and ready-to-use in your assembly.