SynWire – Winding Wires SynWire V 180, Copper Wire, round, enamelled
- Solderable enamelled round cu.wire
- Insulated with polyurethane
- Class 180
SynWire V 180 is a thermal class H enamelled copper wire which can be directly soldered.
The most outstanding characteristics of the wire is the possibilty of efficient and safe contacting of the wire ends by quick and exact soldering at solder bath temperatures from 390 °C upwards without prior mechanical removal of the insulation film. This type of enamelled copper wires fulfills the technical requirements of modern winding techniques and can be well impregnated and cast with compounds in accordance with the manufacturer's instructions. The excellent thermal resistance characteristics offer protection when wire-wound coils have to be compound cast and when subject to short-time overloads. The chemical resistance to aggressive liquid and gaseous mediums is limited, and therefore we recommend that you carry out compatibility tests before using this enamelled copper wire. SynWire V 180 can be easily welded and mechanically connected. Sophisticated process technology and process setting ensure easy mouldability, good elongation plus constant and good insulation characteristics of these wires.
The chemical resistance to aggressive, fluid or gaseous media is limited; therefore, compatibility tests are recommended prior to application.
Application
Contactors, magnetic coils, relays, small motors, transformers, inverters
Standards
IEC / DIN EN 60317-51
NEMA MW 82-C
UL approved
Delivery forms
Grade 1 + 2: 0.036 - 2.0 mm
You have questions according to our winding wires or want to send an inquiry?
Our product manager will be happy to help you.

Dr. Dimitri Jung
Product Manager enamelled copper wire round
+49 5235-968-235 wires@synflex.de
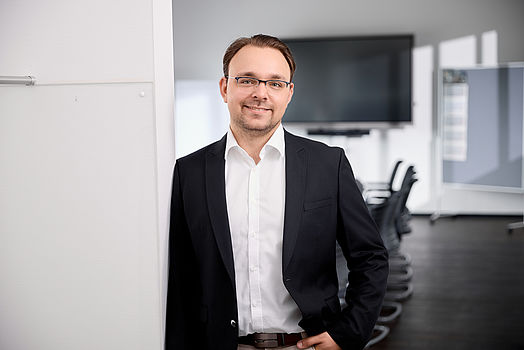
Product Manager enamelled copper wire flat
+49 5235-968-239 wires@synflex.de
Technical data
Typical properties of enamelled round copper wire 0.500 mm, with insulation film grade 1
Property | Unit of measure | Set value | Actual value (typ.) |
---|---|---|---|
Outer diameter with varnish | mm | min. 0.524 - max. 0.544 | as set value |
Bare wire diameter | mm | 0.495-0.505 | as set value |
Adhesion and elongation | mandrel diameter 0.500 mm | 1 x d / 10 % pre-elongation | |
Scrape resistance | N | ≥ 3.100 | ≥6 |
Pencil hardness of varnish | H | 2H - 3H | |
Elongation at break | % | ≥ 28 | ≥ 37 |
Coefficient of friction | µ | / | ≤ 0.140 |
(1) Due to the variety of individual applications we cannot make any generally binding commitments regarding the compatibility. We recommend testing compatibility with the materials being used. |
Property | Unit of measure | Set value | Actual value (typ.) |
---|---|---|---|
Temperature index TI | °C | 180 | 185 |
Cut through temperature (pre-heated block) | °C | 230 | ≥ 230 |
Dielectric loss factor | (°C)(tan δ) | / | ≥140 |
Heat shock at 200 °C | mandrel diameter 1.120 mm | 1 x d / 10 % pre-elongation | |
Solderability at 390 °C | s | ≤ 4 | ≤ 2.5 |
(1) Due to the variety of individual applications we cannot make any generally binding commitments regarding the compatibility. We recommend testing compatibility with the materials being used. |
Property | Set value | Actual value (typ.) |
---|---|---|
Enamel pencil harness after storage ½ h/60 °C in standard solvent | min. H | 2H - 3H |
Enamel pencil harness after storage ½ h/60 °C in alcohol | min. H | H |
Resistance to impregnants (1) | / | yes |
Resistance to commercial refrigerants (1) | / | no |
Resistance to dry transformer oils (1) | / | not recommended |
Resistance to hydraulic oils (1) | / | no |
(1) Due to the variety of individual applications we cannot make any generally binding commitments regarding the compatibility. We recommend testing compatibility with the materials being used. |
Property | Unit of measure | Set value | Actual value (typ.) |
---|---|---|---|
Dielectric strength RT | kV | ≥ 2.4 (twist) | ≥ 3 (cylinder) |
High voltage discontinuities (testing voltage 750 V) | ≤ 10 on 30 m | ≤ 7 on 100 m | |
Electrical conductivity of Cu conductor | MS/m | 58-59 | ≥58.5 |
(1) Due to the variety of individual applications we cannot make any generally binding commitments regarding the compatibility. We recommend testing compatibility with the materials being used. |