SynTherm® – Insulating Materials SynTherm® YT510 DDP
SynTherm® YT510 DDP is a synthetic electro-insulation paper constructed of a calandered, aromatic polyamide fibride flock composition. Both sides of the paper are printed with a B-stage Epoxy resin in a diamond dotted pattern.
The base material SynTherm® YT510 is a Class H (180 °C) insulating material. Temperatures below 200 °C only slightly influence its electrical properties. The good mechanical properties can be extrapolated to significantly higher temperatures. SynTherm® YT510 is also suitable for us at temperatures to -190 °C due to its polymer-structure. It has a high short-term dielectric strength. SynTherm® YT510 is compatible with all classes of common resins, varnishes, adhesives as well as transformer liquids, lubricants, and cooling agents. Common solvents may lead to slight reversible moisture expansion. SynTherm® YT510 has low flammability (UL 94V-0) and very high resistance to beta and gamma radiation.
Application
SynTherm® YT510 DDP is used as layer insulation in transformers.
Standards
- Insulating material class F (155 °C). Base material class H (180 °C)
- The base material is UL listed (RTI mech. + electr. 210 °C)
Delivery forms
Film thickness in μm:
50, 80, 130, 180, 250, 300, 380, 510, 760
SYNTHERM® YT510 DDP is available:
- in tapes: depending on material thickness on request beginning at 6mm (thin material)
- in rolls: 1000 mm
Feathering:
- depth approx. 1 - 12 mm, distance approx. 1 - 10 mm
- 10 mm up to 240 mm width, thickness on request
Base
Calandered, aromatic polyamide fibride flock composition with diamond dotted B-stage resin on both sides.
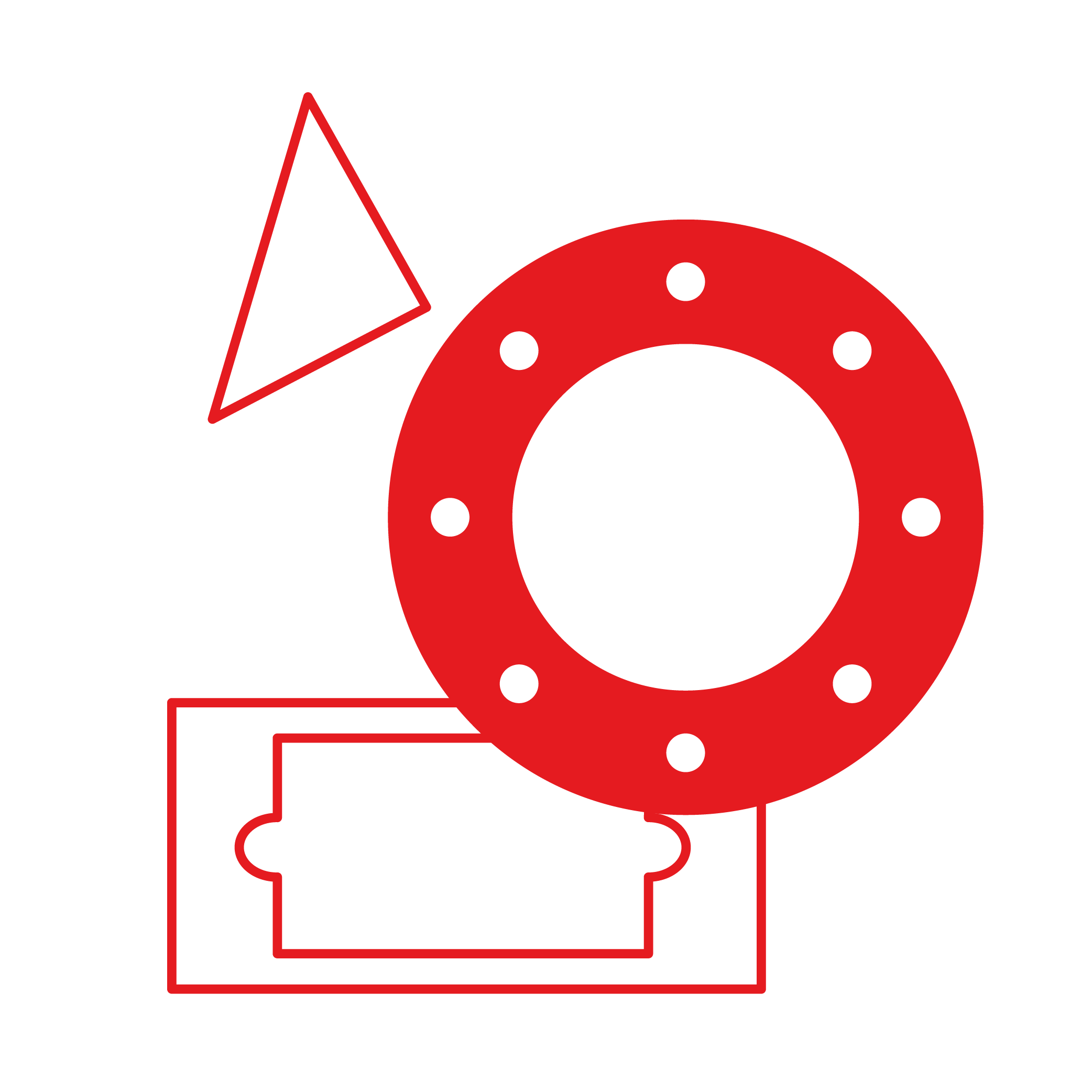
Punched parts, bent & formed parts
We offer a wide range of punched and formed parts: Rolls, individual parts unsorted, sorted or stacked, adhesive on one or both sides, non-adhesive, with or without a grip tab.
More about punched parts
Technical data
Property | Unit of measure | Test standard | |||||||||
---|---|---|---|---|---|---|---|---|---|---|---|
Nominal thickness | μm | 80 | 130 | 180 | 250 | 300 | 380 | 510 | 760 | ||
Typical thickness | µm | 78 | 130 | 180 | 245 | 290 | 365 | 515 | 755 | GB/T451.3-2002 | |
Specific weight | g/m² | 63 | 116 | 175 | 249 | 309 | 390 | 510 | 690 | GB/T451.2-2002 | |
Tensile strength longitudinal | N/cm | 66 | 140 | 225 | 255 | 320 | 380 | 500 | 650 | GB/T12914-2008 | |
Tensile strength transversal | N/cm | 29 | 56 | 105 | 165 | 200 | 260 | 345 | 450 | GB/T12914-2008 | |
Elongation at break longitudinal | % | 8.5 | 10 | 11 | 13.5 | 16 | 13 | 13 | 13 | GB/T12914-2008 | |
Elongation at break transversal | % | 9 | 11.5 | 12.5 | 14.5 | 15.5 | 12 | 13 | 12 | GB/T12914-2008 | |
Shrinkage at 300 °C longitudinal | % | 3.5 | 3.0 | 3.0 | 3.0 | 3.0 | 3.0 | 3.0 | 3.0 | IEC60819-2:2002 | |
Shrinkage at 300 °C transversal | % | 3.0 | 2.5 | 2.5 | 2.5 | 2.5 | 2.5 | 2.0 | 2.0 | IEC60819-2:2002 | |
Elmendorf tear strength longitudinal | N | 1.0 | 2.0 | 3.5 | 5.0 | 6.5 | 10.0 | 13 | - | GB/T455-2002 | |
Elmendorf tear strength transversal | N | 1.7 | 3.3 | 4.8 | 6.0 | 8 | 13.5 | 16 | - | GB/T455-2002 |
Property | Unit of measure | |||||
---|---|---|---|---|---|---|
Thickness increase (one side) | µm | 10±15 % | ||||
Basic weight increase (both sides) | g/m² | 5±10 % | ||||
Curing conditions | h | 1 | 3 | 10 | 20 | 30 |
Curing conditions | °C | 130 | 120 | 110 | 100 | 90 |
Shelf life | 6 months after production |
Property | Unit of measure | Test standard | |||||||||
---|---|---|---|---|---|---|---|---|---|---|---|
Nominal thickness | μm | 50 | 80 | 130 | 180 | 250 | 300 | 380 | 510 | 760 | |
Field intensity | kV/mm | 13 | 14 | 18 | 20 | 22 | 23 | 20 | 18 | 19 | GB/T1408.1-2006 |
Dielectric constant (50 Hz) | 1.5 | 1.5 | 2.1 | 2.4 | 2.5 | 2.7 | 3.0 | 3.1 | 3.2 | GB/T1409-2006 |